
Een Duits consortium van MKB-bedrijven, autofabrikant, Tier 1 toeleverancier én onderzoeksinstituten wil 3D metaalprinten op grote schaal gaan toepassen. Ze gaan zowel bij BMW in München als GKN Powder Metallurgy in Bonn serieproductie voor de automobielindustrie opstarten. Daartoe worden twee bijna volledig geautomatiseerde AM-productielijnen gebouwd. Hierdoor moeten de kosten per geprint onderdeel gehalveerd worden.
Menige AM-expert bestempelt de automobielindustrie als de sector waar 3D printen voor massaproductie op het punt van doorbreken staat. Een consortium van bedrijven en onderzoeksinstellingen rond het Fraunhofer ILT en het Digital Adaptive Production (DAP) in Aken, hebben de aftrap gegeven voor een tweejarig project waarin ze naar serieproductie met additive manufacturing van op z’n minst 50.000 componenten per jaar gaan. Ook willen ze 10.000 losse onderdelen en spare parts gaan 3D printen, in een hoge kwaliteit en onder de extreme kostendruk die de automobielindustrie altijd typeert.
Doel: 50.000 onderdelen per jaar vergaand geautomatiseerd 3D printen
De deelnemers aan het IDAM project.
Geen gereedschappen en mass customization
De twaalf partners in het IDAM project (Industrialization and Digitization of Additive Manufacturing for Automotive Series Processes) willen met 3D metaalprinten zowel kosten als doorlooptijd besparen. Dat denken ze te realiseren doordat er geen matrijzen meer gemaakt hoeven te worden en mass customization tegen nul extra kosten mogelijk wordt. Daartoe gaan ze zowel in München als in Bonn twee identieke, geautomatiseerde AM-productielijnen bouwen. In München is dat bij het AM Center van BMW Group; in Bonn bij GKN Powder Metallurgy, een grote toeleverancier aan de automobielindustrie.
Kosten 3D metaalprinten per onderdeel halveren
Deze modulaire productielijnen dekken de volledige productieketen af: van digitale voorbereiding tot en met 3D printen en post processing. Dankzij het modulaire concept van de lijn kunnen de modules aangepast worden aan de wisselende productie-eisen, die per onderdeel kunnen verschillen. Doordat het hele AM-proces in zijn totaliteit wordt bekeken en vergaand geautomatiseerd, denken de projectpartners het aandeel manuele arbeid fors te kunnen reduceren. Van 35 procent nu naar 5 procent in de toekomst. Mede hierdoor moet de kostprijs per 3D geprint product gehalveerd worden.
BMW past 3D metaalprinten al toe in de serieproductie van de I8 roadster. Hier lees je meer over deze toepassing van AM.
Belangrijke rol voor MKB-bedrijven
Het Fraunhofer ILT benadrukt in een toelichting op het IDAM project de rol van de MKB-partners. Zij ontwikkelen en bouwen de modules voor de AM productielijn. Ook nemen ze de automatisering op zich. Dit zijn onder andere Volkmann uit Soest, Schmitz Specialmaschinenbau uit Rheinbreitbach, ingenieursbureau Kinexon uit Bad Neuenahr en Myrenne uit Roetgen, eveneens een speciaalmachinebouwer met een lange ervaring met 3D printen. Vanuit de AM-industrie is Aconity uit Herzogenrath betrokken, de 3D printerfabrikant die voortgekomen is uit de onderzoeksactiviteiten van het Fraunhofer ILT. De deelname van GKN en BMW zorgen ervoor dat de productielijnen onder echte automotive omstandigheden getest kunnen worden.
Foto boven: een voor de sterkte geoptimaliseerd differentiaalhuis, ontwikkeld door GKN Powder Metallurgy en Porsche Engineering.
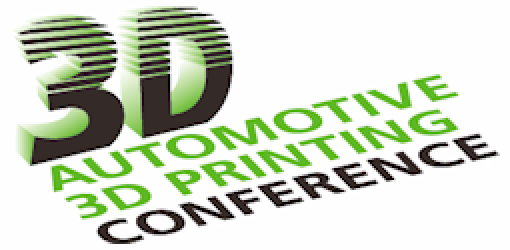
Wil je meer weten over 3D printen voor de automobielindustrie, op 5 juni is er op de Automotive Campus in Helmond de Automotive 3D Printing Conference.