
ASCO toont deze week samen met SLM Solutions een 3D geprinte bracket voor de leading edge flap op de Britse luchtvaartshow Farnborough International Airshow. De inzet van 3D metaalprinten zorgt voor een gewichtsbesparing van 31%.
ASCO en SLM Solutions tonen resultaat op Farnborough International Airshow
Het onderwerp additive manufacturing krijgt dit jaar meer aandacht op de Britse luchtvaartshow, die afwisselend met die in Parijs plaatsvindt. SLM Solutions neemt dit jaar voor de eerste keer deel en laat met het door ASCO ontwikkeld onderdeel meteen zien waarin de voordelen van 3D metaalprinten voor de vliegtuigindustrie zitten: kosten, tijd en gewicht.
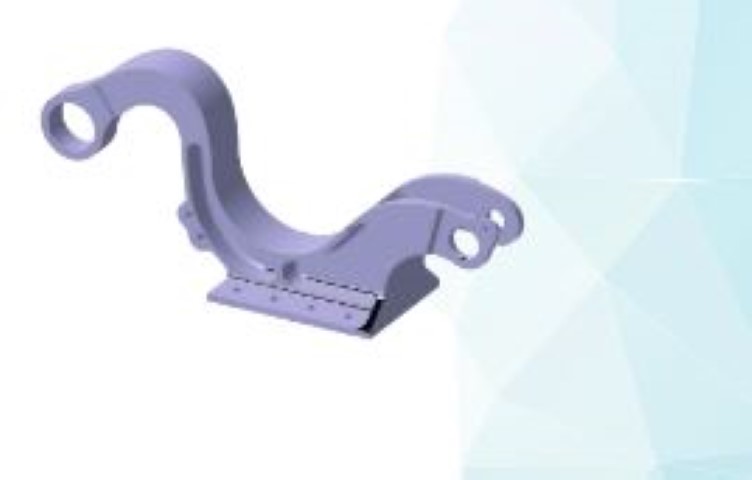
Drie voordelen
Het Belgische ASCO Industries, dat dit najaar wordt overgenomen door de Amerikaanse klant Spirit AeroSystems, heeft een bracket ontwikkeld voor het mechanische deel van een leading edge flap, de klep aan de voorzijde van de vleugel. Het gaat hier om een constructiedeel van het vliegtuig. ASCO heeft samen met SLM Solutions het onderdeel redesigned voor 3D metaalprinten op de SLM-machine met twee lasers, de SLM 280 Twin. Als materiaal is Ti6Al4V gebruikt, een in de luchtvaartindustrie gangbare titaniumlegering. Uiteindelijk levert dit in het productieproces een veel betere buy-to-fly ratio (van 17 naar 1,5) dan wanneer het onderdeel uit vol materiaal wordt gefreesd én een flinke gewichtsbesparing. Het 3D geprinte onderdeel weegt 31% minder: 1416 gram tegenover 2050 gram voor de gefreesde versie. Vliegtuigbouwers zijn vooral hierin geïnteresseerd, omdat elke kilo gewichtsbesparing over de levensduur van een vliegtuig grote hoeveelheden kerosine bespaart.
Waarom 3D printen?
De productietijd op de SLM 280 Twin bedraagt 24 uur per onderdeel, waarna nog slechts minimale nabewerking nodig is. Het oorspronkelijke deel vereiste 4,5 uur freestijd op de machine. De assemblagetijd vervalt echter door het 3D printen van het onderdeel in één geheel. De reden om dit deel te gaan 3D printen is onder andere dat het oorspronkelijke ontwerp lastig te verspanen valt. Bovendien heeft het een slechte buy-to-fly ratio, wat onder andere materiaalverspilling betekent.
Foto’s: ASCO / SLM Solutions
In de Benelex vertegenwoordigt EKZO de Duitse fabrikant van 3D metaalprinters
1 gedachte over “ASCO 3D print leading edge bracket: 31% gewichtsbesparing”
Reacties zijn gesloten.